[From the Scene] Extreme climates to battery cells: Inside Hyundai's safety efforts
By Moon Joon-hyunPublished : March 31, 2024 - 13:56
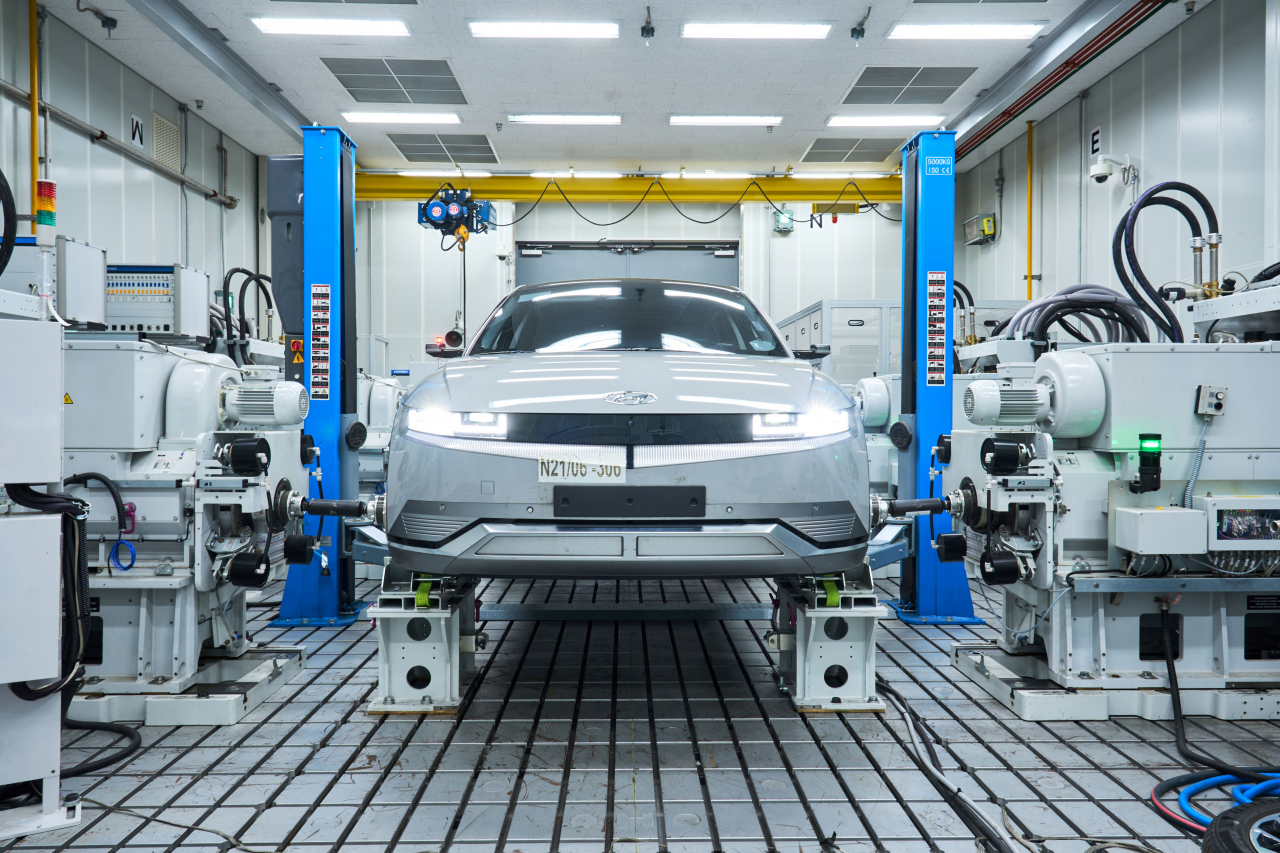
Hyundai Motor Group, having climbed to the rank of the second-largest electric vehicle seller in the United States last year just behind the trailblazer Tesla, recently took reporters behind the scenes to reveal the backbone of their success: a commitment to safety amid the industry's sprint toward longer battery ranges and fast charging.
On Wednesday, the press was invited to the automaker's Namyang Technology Research Center in Hwaseong, Gyeonggi Province, to witness firsthand the safety testing conducted there.
A standout feature of the center was the Commercial Eco-Vehicle Simulation Chamber, which can simulate real-world climate conditions for both internal combustion and eco-friendly vehicles. Inside the largest chamber of its kind in the world, which measures 20 meters in length, 10 meters in width, and 6.6 meters in height, an Xcient hydrogen-electric truck caught attention.
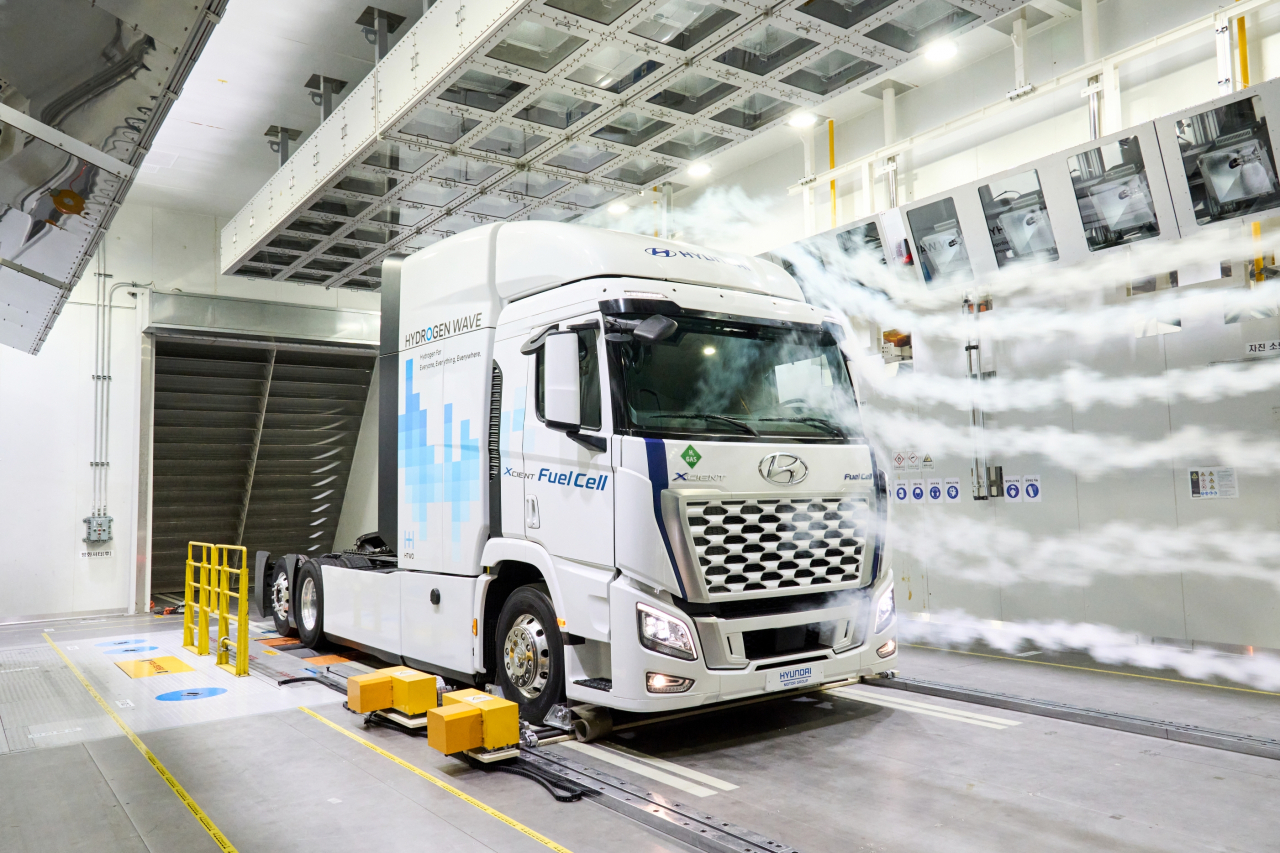
“The beauty of this chamber is its ability to mimic virtually any climate on Earth, from freezing cold at minus 4 degrees Celsius to a scorching 60 degrees Celsius and humidity ranging from a dry 5 percent to a very moist 95 percent. Plus, with our 3.3-meter fan cranking up speeds to 120 kilometers per hour, we can bring extreme real-world conditions indoors,” explained a lab official on the site.
When The Korea Herald reporter entered the chamber, it was set to 45 degrees Celsius to mirror the typical testing conditions for the Middle East market. This setup helps replicate the greenhouse effect observed in vehicles exposed to such temperatures, also aiding in the testing process for models sold in the United States.
For EV development, the chamber’s utility extends to testing battery charging and cooling performance, facilitated by three 400-kilowatt ultra-fast chargers.
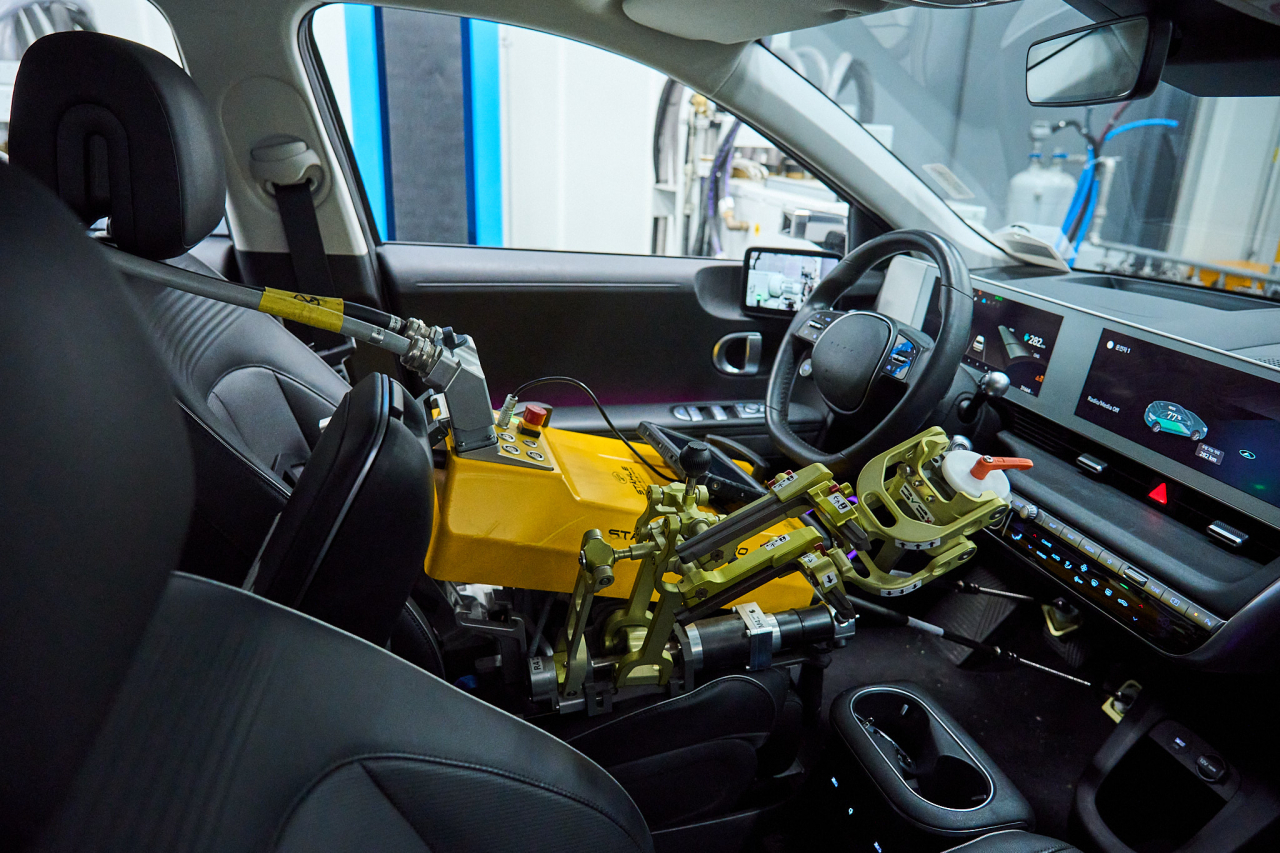
The heart of electrification is embodied in the Electrification Test Center. Here, the focus is on perfecting the quality of EVs by rigorously testing key components like motors and inverters before these cars hit the mass market.
“Here, the entire power system undergoes simulations from a leisurely drive in the countryside to the hustle and bustle of urban commuting,” said Kwak Ho-cheol, head researcher of the electrification drive test team.
The center houses three specialized labs, each designed for a specific phase of vehicle development. The single-axis lab focuses on the early development of motors and inverters, ensuring these components meet global standards. The two-axis lab is all about using reducers and driveshafts to mimic the complex mechanism of a vehicle in motion.
Lastly, the four-axis test subjects an actual vehicle, such as the Hyundai Ioniq 5, with the car's real battery and drivetrain to lifelike scenarios. Robotic technology adds a futuristic twist, with robots stepping into the shoes of human drivers, executing everything from gear shifting to nuanced braking and accelerating.
There is also meticulous work being done at the Battery Analysis Laboratory. This lab delves deep into EV batteries, analyzing their performance and durability in a specialized dry room.
“In our line of work, even a little bit of moisture can mess up the sensitive materials within the batteries. That's why we go to great lengths to keep our analysis rooms dry and our data accurate," said Lee Jae-wook, Hyundai's battery materials analysis team leader.
"We are essentially doing additional testing on the batteries supplied by our partners,” he added.
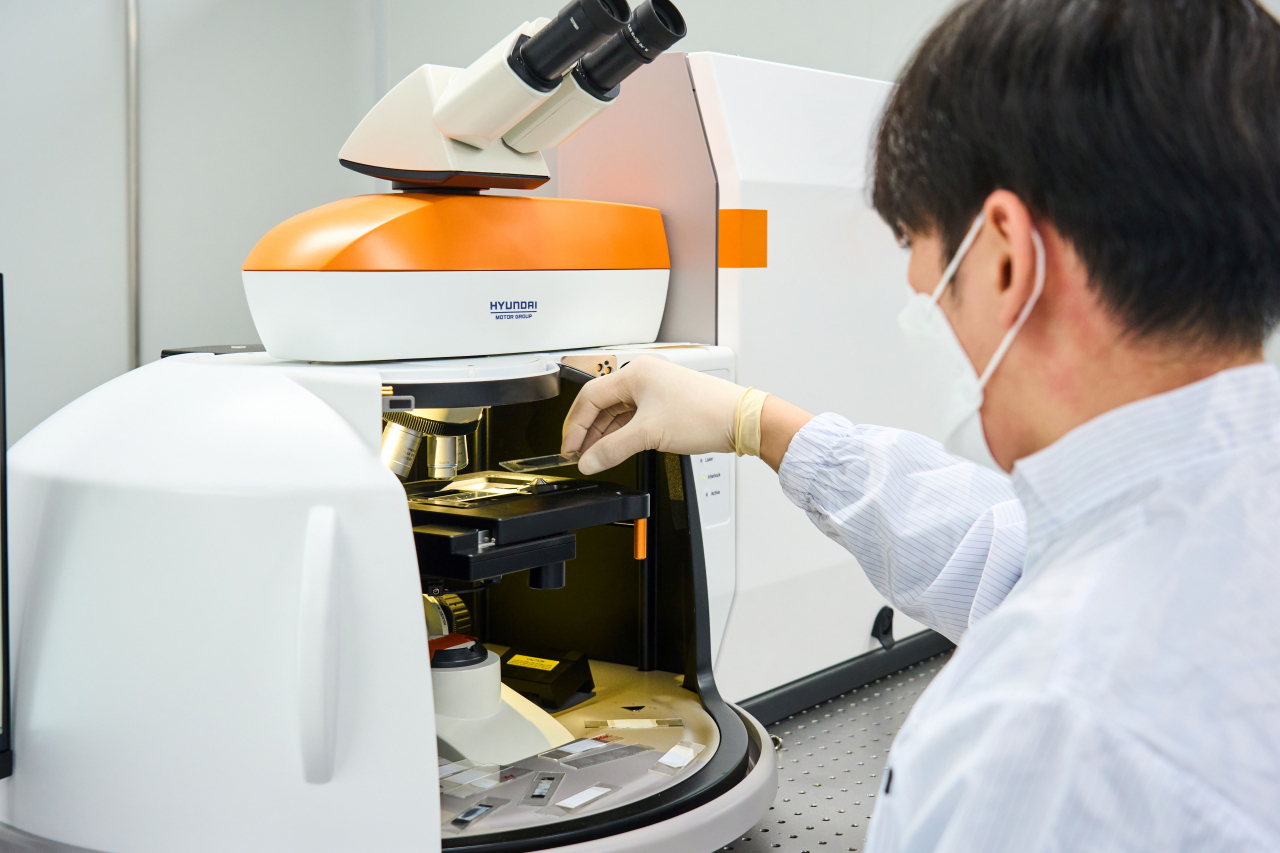
In the main analysis room, tools like the Raman spectrometer come into play, using laser light to reveal how the battery's materials are bonded together, similar to using a microscope to see the cells in a leaf, allow scientists to understand the materials' properties on a microscopic level. Such insights are crucial for predicting how batteries will perform in unexpected conditions,
This tour is not Hyundai's first public showcase of its Namyang facility. Last year, the company demonstrated crash tests of the Ioniq 5 EV on the site.
“Last year, we even set up a dedicated space for battery cell dismantling to get ahead of any potential fire risks. Our team will continue to double down on the basics like safety and reliability, not just driving range or performance," said Jung Yi-deun, from the materials analysis team.